ASME CRTD-103:2014 pdf download CONSENSUS ON BEST TUBE SAMPLING PRACTICES FOR BOILERS & NONNUCLEAR STEAM GENERATORS
Following tube removal, a new tube will need to be reinstalled. It is critical that the replacement tube be consistent with the original specification on the diameter, wall thickness,and material designation.In HRSG units, it can be difficult to install a replacement finned tubesection. In such cases,contact with the HRSG manufacturer is suggested regarding appropriatetube replacement procedures or baffling requirements.
To minimize overlapping flow effects of the upstream and downstream replacement weldsduring operation, ensure that the tube segment reinstalled in the boiler or HRSG is over 15internal diameters in length.
Tube Sample ldentification
Always mark the tube exterior with the location (such as tube number and row) and orientation (such as top and bottom) prior to removal so that this information is not lost once thetube has been removed. It is also good to indicate the hot and cold sides of the tube, if applicable.lf fireside attack is suspected, avoid writing on areas of attack by taking a longer tube sample andmarking above or below the area to be analyzed.
Many facilities use directions (North, South, East, and West) to designate locations within aboiler.Unfortunately, those who are not familiar with the particular boiler or HRSG, will notunderstand the significance of this nomenclature.Therefore, the terms Front,Rear, Left, andRight should be used to identify the HRSG or boiler tube sample location.If compass directionswere previously used to describe location in past sample sets, specify which direction
corresponds to the front of the boiler or HRSG to help compare current and past data.
For field erected water tube boilers and HRSG units, the rear of the furnace is always theend of the unit with the exhaust stack. The front of the unit is the opposite end from the rear.Front, rear, left and right directions are from the perspective of someone standing at the front andlooking at the boiler or HRSG unit.
For package, water-tube steam boilers, the burners are located in the front wall of the boiler.The boiler exhaust can be at the front or rear of the boiler – depending on the boiler design.
For fire tube boilers, the front of the boiler has the burner. In most fire tube boilers, theboiler is fired from the front side; the furnace gas passes down through a set of tubes to the rearof the boiler and then returns to the front of the boiler through another set of tubes. In this design,the exhaust stack happens to be at the front of the boiler. As with water tube boilers, directions offront, rear, left and right directions are from the perspective of someone standing at the front andlooking at the boiler.
Sometimes tabs or rings have to be welded to the tube sample to keep the tube from fallingwhen the last cut is completed.If a tab is required, use light tack welding and do not weld nearfailure locations or other areas of importance.Also, weld on the cold side rather than hot side forsamples collected for deposit weight assessments.
During tube extraction, do not use hammers or pry bars, if possible, since these can dislodgesignificant amounts of deposit.
Billing company name and address if different than the facility of origin.
Steam generator/boiler designation (e.g., Boiler 1, HRSG 3)
Work desired.
Date results needed. This will indicate the level of priority for the analysis. Most laboratories have a variable cost structure depending on how fast the results are required.
General type of tube (e.g., waterwall, nose, screen, generation bank, floor, roof, division wall, HP evaporator, etc.).
General location (left furnace, first pass tube, etc.).
Wall (front, rear, left, right) for waterwall tubes.
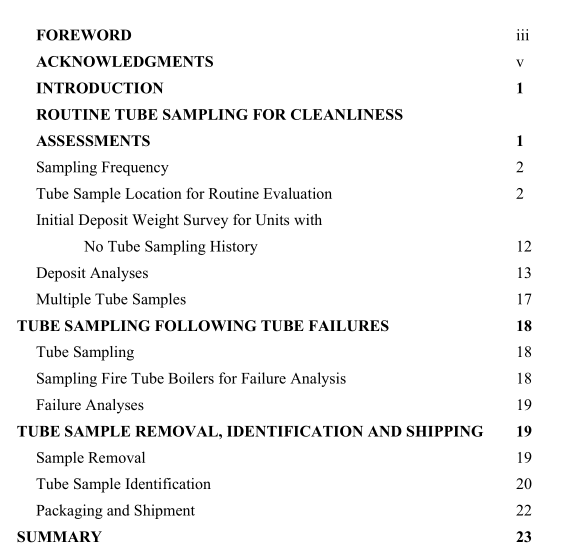