ASME RAM-2:2016 pdf download Reliability, Availability, and Maintainability Program Development Process for Existing Power Plants
INTRODuCTION
A reliability, availability, and maintainability (RAM)program is a structured way to identify and deliver theRAM requirements of a power plant in the most cost-effec-tive manner. This Standard provides guidance for theprogram implementation portion of the RAM processdescribed in ASME RAM-1.It is intended to implementa comprehensive availability assurance program. ThisStandard is intended for existing facilities.
2 sCOPE
This Standard amplifies and clarifies the requirementsof ASME RAM-1 for implementing a RAM program for apower-generation facility.This Standard assists in devel-oping program goals, identifying a master equipment list(MEL) to load into the enterprise asset managementsystem (EAMS),and populating scheduling systemswith finished content as complete work orders that areready to perform work.A RAM program includes hierarch-ical breakdown of the facility, tagging of equipment (i.e.,components), risk categorization of systems and equip-ment tags, development of common standards for compo-nents, and customization for similar context locations inthe plant. This Standard finalizes work organization astask lists in work orders, routes, and rounds. It providesa process to implement ASME RAM-1 based on termi-nology and methodology used in power plants.
This Standard addresses the following:
(a) equipment assessment for risk(b) asset tagging
(c) template selection and application
(d) equipment asset management software
(e) development and organization of work (e.g, devel-opment of operating procedures, rounds, and workorders)
fRAM program plans
lg) training required to implement the program
3 PURPOSE
The purpose of this Standard is to provide informationto enable plant personnel to develop an effective RAMprocess in accordance with ASME RAM-1.An effectiveRAM program ensures that critical plant equipmentperforms cost-effectively as intended by design. ThisStandard provides an all-encompassing RAM support process that develops simple,clearly worded RAManalysis in accordance with ASME RAM-1.
4DEFINITIONS
The following is a list of terms relating to the implemen-tation and use of RAM programs:
age exploration: systematic examination of the lifetime acomponent or part can support in an application in-service.
coding scheme: an often mnemonic scheme that assignsequipment codes or tags; the scheme usually embedsthe plant,unit, system, component type, numberedsequence of the component and higher-tier equipmentof which the component is a part (system), subsystem,and perhaps additional information. Each plant requiresa common coding scheme.
complex equipment:
(a) equipment that displays many unique combina-tions of parts, failure modes,and failure causes, noneof which is predominant in failure of its functions.
(b) equipment that displays random failure patternsin-service. See also simple equipment.
contextual risk map: a map of all master equipment list(MEL) component tag information, customized withcomponent risk information.
critical: likely to cause functional failure directly; failing ahigh-level performance goal in single fault.
custom template: an application of a standard templatebased upon one context,e.g., a standard template main-tenance plan customized for one location. See standardtemplate.
direct failure criteria: criteria limiting criticality risk clas-sification to the failures that, with only a single occurrence,have the ability to affect operating goals.This criteriafocuses scheduled maintenance resources and effortswhere they will do the most good.
diversity: the use of different methods to achieve func-tional but not exact physical redundancy within a RAMprogram.
dominant failure mode ( DFM): a likely failure mode of acomponent or part; it is considered in the design of thecomponent or part and addressed in the maintenanceplan.
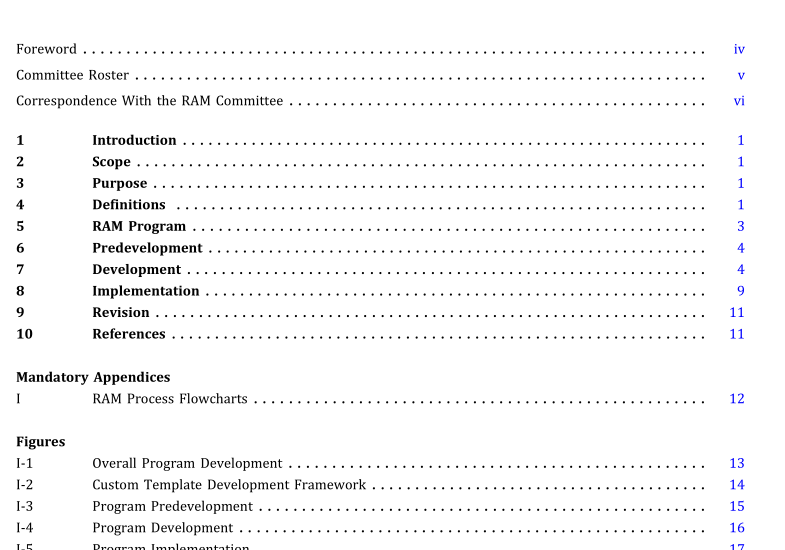